Opening the Power of Welding WPS: Methods for Effectiveness and Safety in Manufacture
In the world of manufacture, Welding Procedure Requirements (WPS) stand as the foundation of welding operations, dictating the required steps for achieving both efficiency and safety in the fabrication process. Understanding the intricacies of WPS is paramount to using its complete capacity, yet numerous organizations have a hard time to unlock the true power that lies within these documents (welding WPS). By diving right into the techniques that optimize welding WPS, a globe of improved productivity and increased security awaits those going to discover the subtleties of this important aspect of manufacture

Importance of Welding WPS
The relevance of Welding Procedure Specs (WPS) in the manufacture industry can not be overemphasized. WPS work as a vital roadmap that lays out the required steps to make certain welds are done regularly and correctly. By specifying important criteria such as welding processes, products, joint styles, preheat temperatures, interpass temperatures, filler steels, and post-weld warmth treatment requirements, WPS give a standardized strategy to welding that improves performance, top quality, and safety and security in construction procedures.
Adherence to WPS aids in attaining harmony in weld top quality, reducing the chance of defects or structural failings. This standardization additionally facilitates compliance with sector policies and codes, making certain that produced structures satisfy the needed security criteria. Furthermore, WPS paperwork makes it possible for welders to replicate effective welding procedures, bring about consistent results across various projects.
Essentially, the careful development and stringent adherence to Welding Treatment Requirements are extremely important for promoting the honesty of bonded structures, protecting versus possible threats, and upholding the track record of construction business for delivering top quality services and products.
Crucial Element of Welding WPS
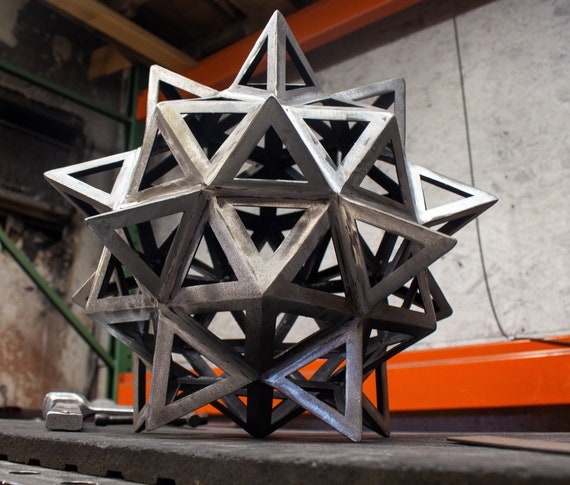
Enhancing Efficiency With WPS
When enhancing welding procedures, leveraging the crucial elements outlined in Welding Procedure Specifications (WPS) becomes necessary for improving procedures and taking full advantage of productivity. One method to enhance effectiveness with WPS is by thoroughly choosing the suitable welding specifications. By adhering to the particular guidelines offered in the WPS, welders can make certain that the welding equipment is established up properly, causing top notch and consistent welds. Furthermore, complying with the pre-approved welding sequences described in the WPS can considerably lower the moment invested on each weld, eventually enhancing overall performance.
On a regular basis evaluating and updating the WPS to include why not try these out any type of lessons learned or technical improvements can also add to effectiveness improvements in welding procedures. By accepting the standards set forth in the WPS and continuously looking for means to optimize processes, producers can attain greater efficiency levels and exceptional end outcomes.
Ensuring Security in Manufacture
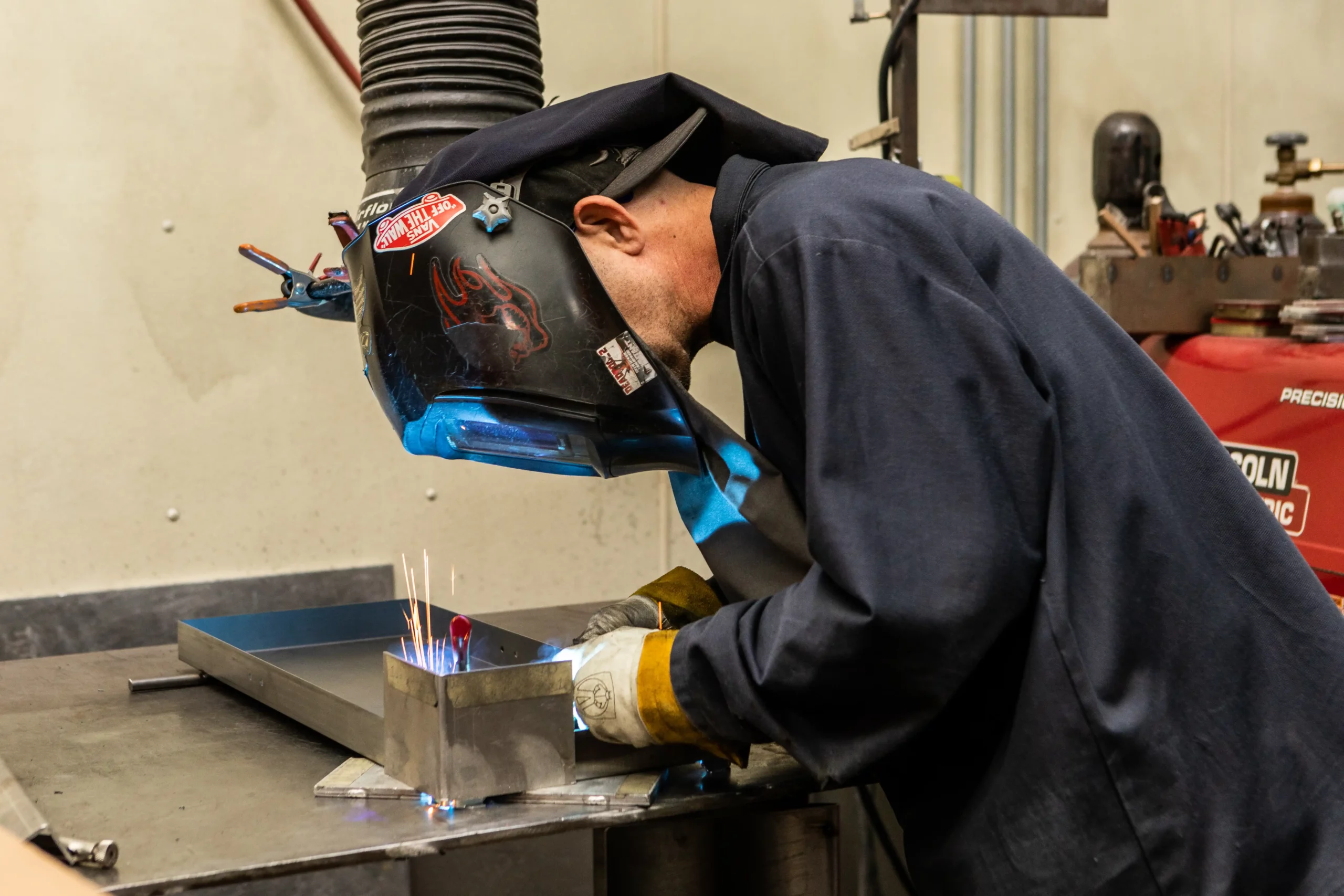
Ensuring safety and security in construction includes a multifaceted approach that encompasses numerous aspects of the welding procedure. Welders should be outfitted with suitable equipment visit site such as safety helmets, handwear covers, and protective apparel to reduce threats connected with welding tasks.
Furthermore, adherence to correct ventilation and fume removal systems is essential in keeping a healthy work environment. Welding fumes contain unsafe compounds that, if inhaled, can posture major wellness risks. Carrying out effective ventilation procedures helps to lessen exposure to these harmful fumes, promoting breathing wellness among workers.
Routine equipment upkeep and inspections are likewise essential for making sure safety in construction. Damaged machinery can bring about injuries and mishaps, underscoring the relevance of regular checks and timely repair services. By focusing on safety steps and fostering a culture of awareness, fabrication facilities can develop a effective and protected job setting for their personnel.
Executing WPS Ideal Practices
To enhance functional efficiency and make sure quality outcomes in manufacture processes, including Welding Treatment Specification (WPS) finest techniques is critical. Selecting the suitable welding procedure, filler material, and preheat temperature level specified in the WPS is crucial for attaining the desired weld top quality. Making sure that qualified welders with the essential accreditations lug out the welding treatments according to the WPS standards is important for uniformity and dependability.
Verdict
In final thought, welding WPS plays an important duty in guaranteeing performance and safety in manufacture procedures. By focusing on essential components, improving effectiveness, and implementing finest techniques, companies can enhance their welding procedures. It is vital to prioritize safety and security measures to prevent accidents and guarantee a pop over to these guys smooth manufacturing process. By following these methods, organizations can open the complete possibility of welding WPS in their fabrication operations.
In the realm of manufacture, Welding Treatment Specifications (WPS) stand as the backbone of welding operations, determining the necessary steps for achieving both efficiency and safety in the fabrication procedure. By specifying crucial criteria such as welding processes, materials, joint designs, preheat temperatures, interpass temperature levels, filler steels, and post-weld heat therapy needs, WPS supply a standardized method to welding that enhances efficiency, top quality, and safety and security in manufacture procedures.

When optimizing welding procedures, leveraging the key elements laid out in Welding Procedure Requirements (WPS) becomes necessary for maximizing and improving processes performance. (welding WPS)
Comments on “Advanced Welding WPS: Tailoring Requirements for Complex Jobs”